【转载】DCS、MES、ERP在化工企业的应用及发展
声明:本站鼓励原创行为,本文因为转载众多没找到原作者,版权归原作者所有。
【摘 要】在信息时代,企业的发展依靠的是对高质量水平信息的获取,化工企业更是如此。DCS、MES、ERP三系统在化工企业中发挥着十分重要的作用,而今后将它们进行有机的结合,对企业领导者的科学决策,实现资金流、信息流、物流和控制流四流合一具有着十分重大的作用,而这也正是现代化工企业建设的目标。
中国论文网 http://www.xzbu.com/8/view-3474622.htm
【关键词】化工企业;DCS;MES;ERP
在信息时代,企业的发展依靠的是对高质量水平信息的获取,化工企业更是如此。随着我国国内化工企业与国外大型化工企业的竞争日益激烈,要提高我国化工企业竞争力,必须要从信息化方面入手。化工企业是典型的流程控制行业,内部可分为过程控制层,生产执行层,经营管理层。因此对DCS、MES、ERP三系统进行分析,对我国化工企业信息化建设具有一定的促进作用。
1 ERP、MES、DCS发展及关系
1.1 ERP、MES、DCS的含义及发展
ERP系统是一种操作平台和管理信息系统,利用该系统可以将企业内的各种资源充分利用起来,对于提高企业整体运作效率,降低库存具有明显的作用。传统的ERP系统中,供应链系统是这个企业运行的基础,结果就形成了生产计划和执行系统处在了供应链的核心地位,对供应链的运行造成直接影响。而目前的ERP系统则更注重对企业外部重要环境的诸如市场、企业取向等不确定性因素的研究,并且对于外部不确定性因素的把握也就成了ERP成功的关键。MES系统就是俗称的生产管理系统,1990年由AMR组织提出并使用。该系统在提出的初期,注重的是生产现场信息的整合等。而在上个世纪90年代中期,对MES提出了标准化,功能化以及模块化的思路,此时,许多MES软件也多实现了组件化,对集成和整合提供了较大的便利,甚至于企业还可以根据自身需构建合适的MES系统。MES系统并不是只面向生产现场的系统,其还起到了连接现场层和经营层,对他们的信息进行双向传递的作用的系统。DCS系统也称集散控制系统,其具有十分先进的过程管理和控制运算功能,其对生产运行提供最直接的实时数据。该系统自1975年问世以来,经历了近30年的发展,虽然系统的体系结构没有发生大的改变,但经过不断的发展和完善,其功能已经更加开放、标准和产品化。
1.2 DCS、MES、ERP之间的关系
ERP对企业而言是企业的资源计划,针对的是企业的人力资源,生产资源,财务资源等进行计划,从而提高企业中有限资源的利用效率。而MES则侧重于对企业生产计划的制定和物料需求计划制定等,实现的是对制造现场的控制,通过将企业生产计划进行细化分解,实现对生产作业的有效管理和调度。而DCS系统则是通过其对生产工艺参数的实时采集统计、报表打印、优化报警的功能,实现降低能源和原材料的消耗,从而提高产品的质量,保障安全生产的同时又减轻了一线员工的劳动强度。这三个系统在企业中是十分重要的,特别是对于化工企业而言,可以实现关系型数据库和实时数据库之间信息的交流,保证了企业对信息的集成。其关系可以如此认为:ERP侧重企业计划层,属于企业级管理系统,MES侧重于执行层,主要针对的是企业制造过程中的管理,而DCS则侧重于对现场设备的控制,主要是面向于生产作业现场。而要将这三个系统整合起来,则需要通过MES担负的桥梁关系才可以实现。
2 DCS、MES、ERP在化工企业中的应用和发展趋势
2.1 DCS、MES、ERP在化工企业中的应用
ERP系统在化工企业中的应用是从整合资源、信息共享、集中管理入手,对公司的管理不断深入和扩张的需要,使经营者能够对各项经营指标进行分析,做到对经营的有效管控,从而提升管理水平。实施ERP系统对化工企业具有十分重要的作用,首先在网络技术的帮助下,建立起了化工企业的数据共享和及时管理信息的平台,从而提高企业运作效率和相应速度。其次通过统一规范的流程处理平台,实现了业务联动、运作高效流程化,使得企业整体业务协调有序,对信息的反应速度迅速。第三,加强了计划的准确与执行力度,而且也强化了企业的集中管理。MES系统在化工领域,通过以面向数据的模型为核心系统,将关系数据库和实时数据库连接起来,从而起到了对化工生产的控制和诊断、单元整合、物料平衡、过程监视、环境监测、生产计划、调度、排产、离线在线模拟与优化等操作管理。从而比较好的将化工企业综合自动化系统中管理与生产双重性质的信息的问题解决了。不过目前,我国化工企业对MES的应用目前还未实现,如西方发达国家一般作为化工企业综合自动化系统理论和产品的主流框架,还处在初级发展阶段。DCS系统在化工系统中应用的关键是实现各生产设备之间的通信,其任务是为生产设备所有部件提供通讯网络,通过对生产一线的监控,实现随生产一线各类信息的收集、集成和控制,比如在化工生产过程中,做到对反应器反应温度的控制,液位串级控制和连锁控制等,其对信息的收集具有实时性,而且在生产过程中,还能够对相关参数进行调整,另外通过创建报警服务,在生产过程中,还可以对生产设备和运行状态进行警报监视。
2.2 DCS、MES、ERP在化工企业中的发展趋势
我国化工企业要实现新发展,必须要对企业进行信息化建设。而将DCS、MES、ERP三个系统进行有机结合,可以实现化工企业的“管控一体化”。通过将其有机整合,可以使化工企业的经营计划、采购、库存、财务、物料需求计划等做到动态的监控,实现对物流、信息流、控制流和资金流的四流合一。化工企业的生产运行和管理,需要依靠一系列应用系统来支撑,而DCS、MES、ERP三个系统则是化工生产过程中最为核心的几个系统,未来企业要实现信息化,必然要求经营管理层(ERP),生产执行层(MES),现场设备控制层(DCS)攘括了整个生产过程的信息的收集和整理。进而提高我国化工企业信息化水平,提高化工企业竞争力。
小结
DCS、MES、ERP三系统在化工企业中发挥着十分重要的作用,而今后将它们进行有机的结合,对企业领导者的科学决策,实现资金流、信息流、物流和控制流四流合一具有着十分重大的作用,而这也正是现代化工企业建设的目标。
参考文献
[1]王兆录,李会芹,仲红军 DCS系统在化工企业应用中的几个问题[J] 山东化工 2004(33)
[2]刘芳. ERP系统在化工企业中的实施及效益分析[J]. 现代商贸工业. 2009(15)
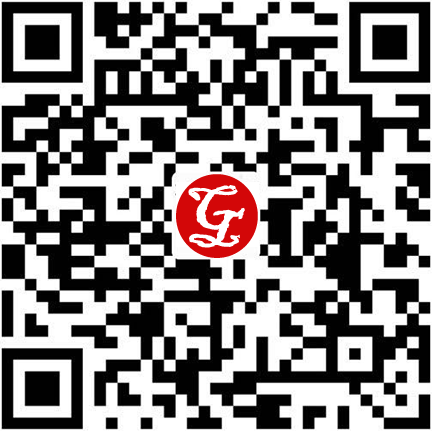
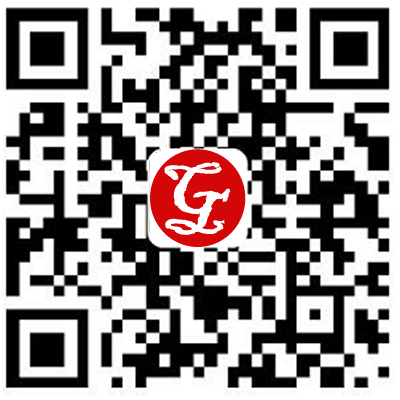
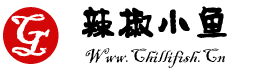
共有 0 条评论